Revolutionizing Foam: UT Dallas Researchers Unleash Durable, Recyclable 3D-Printed Foam
- Aniksha Kar
- 12 minutes ago
- 3 min read
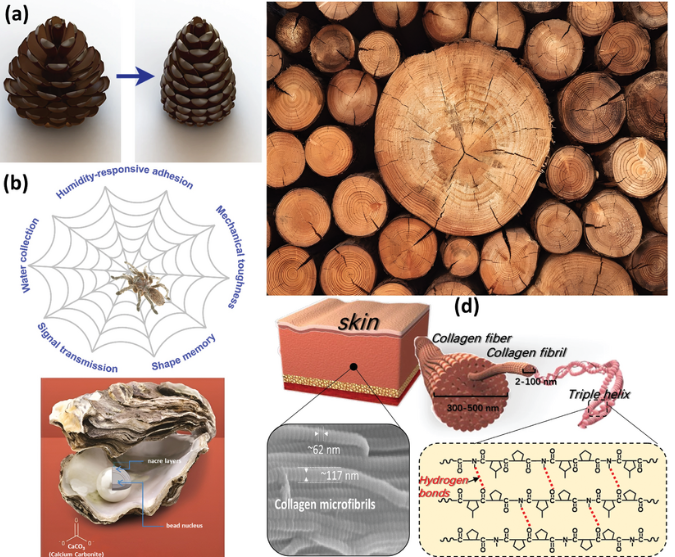
Foam is ubiquitous, silently supporting our daily lives from the comfort of our mattresses to the safety of our car seats. Yet, traditional polymer foam poses a significant environmental challenge due to its non-recyclable nature. Now, researchers at The University of Texas at Dallas have unveiled a groundbreaking innovation: a 3D-printed foam that is not only more durable but also more recyclable, promising to transform industries and reduce waste.
The Challenge of Traditional Foam
Most commercially available foam is thermoset, meaning it undergoes a chemical reaction that permanently solidifies its structure. This irreversibility renders it impossible to reshape, melt, or dissolve, leading to a substantial accumulation of non-recyclable waste in landfills.
A Novel Approach: Dynamic Covalent Chemistry and 3D Printing
The UT Dallas team, led by Dr. Ron Smaldone, associate professor of chemistry and biochemistry, and doctoral students Rebecca Johnson BS’20 and Ariel Tolfree BS’23, tackled this challenge by leveraging 3D printing and dynamic covalent chemistry.
3D Printing for Customization: The 3D-printing process allowed the researchers to create complex, customized shapes, a feat difficult to achieve with traditional foam manufacturing. To demonstrate their proof-of-concept, they printed a whimsical balloon dog, showcasing the intricate structures possible with their new foam.
Dynamic Covalent Chemistry for Durability and Recyclability: Unlike thermoset foams, this new foam utilizes reversible bonds, enabling self-repair when damaged. While not fully meltable like thermoplastics, these bonds significantly enhance the material's lifespan and versatility.
The Research Journey: Perseverance and Innovation
Rebecca Johnson, co-lead author of the study, described the project as a two-year endeavor, emphasizing the challenges of formulating a polymer compatible with 3D printing. "This is probably the longest project I’ve ever done," she shared. The team's dedication paid off, resulting in a robust and lightweight foam with exceptional properties.
Applications and Potential Impact
The potential applications for this innovative foam are vast.
High-Impact Absorption: The foam's durability makes it ideal for protective gear such as motorcycle and football helmets, car bumpers, and even armor.
Insulation: The foam's lightweight and customizable structure make it suitable for advanced insulation applications.
Versatile Manufacturing: 3D printing allows for the creation of complex lattice structures, enhancing the material's flexibility and adaptability.
Addressing Sustainability
Ariel Tolfree, who plans to build upon Johnson's work, is focusing on enhancing the foam's recyclability and exploring its sustainability potential. This research aligns with the growing need for eco-friendly materials and manufacturing processes.
The Team's Vision
Dr. Smaldone emphasized the novelty of using dynamic chemistry to create a high-quality foam material. The next phase of research will focus on tuning the foam's properties to meet diverse application needs.
Tolfree's analogy of the balloon dog underscores the transformative nature of their work: "A balloon seems ordinary until it’s twisted into something new, almost defying expectations. Our foams are the same — unassuming at first, but once expanded and transformed, they become something remarkable."
Looking Ahead
This breakthrough by the UT Dallas researchers marks a significant step towards sustainable and high-performance foam materials. As research progresses, we can anticipate a future where 3D-printed, recyclable foams play a crucial role in various industries, minimizing waste and enhancing product performance.
Further Exploration
For a deeper dive into their research, check out the study published in RSC Applied Polymers and their informative YouTube video. This work highlights the power of interdisciplinary collaboration and the potential for innovation to address pressing environmental challenges.
Co-Authors:
Gustavo Felicio Perruci (Mechanical Engineering Doctoral Student)
Lyndsay Ayers BS’24 (Chemistry Doctoral Student)
Niyati Arora (Chemistry Doctoral Student)
Emma Liu (Chemistry Senior)
Vijayalakshmi Ganesh BS’23
Dr. Hongbing Lu (Professor of Mechanical Engineering)
This research stands as a testament to the power of scientific innovation and the potential to create a more sustainable future.
Comments