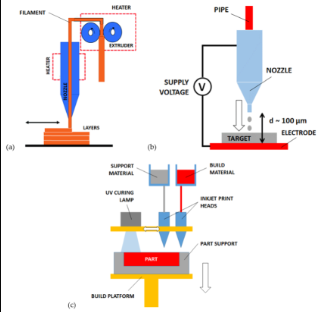
Micro Electric-Mechanical Systems (MEMS) have long been at the forefront of miniaturized technology, enabling a wide range of applications from sensors and actuators to biomedical devices and consumer electronics. However, as the demand for even smaller, more sensitive, and more efficient devices grows, researchers are turning their attention to the realm of Nano Electric-Mechanical Systems (NEMS). In this blog, we delve into the evolution of MEMS to NEMS and the role of 3D printing in advancing micro-scale technology to new frontiers.
Understanding MEMS and NEMS:
MEMS are miniaturized systems that integrate mechanical and electrical components at the microscale, typically ranging from a few micrometers to a few millimeters in size. These systems utilize principles of microfabrication to create structures such as sensors, actuators, and resonators with high precision and functionality.
NEMS, on the other hand, take miniaturization to the next level by operating at the nanoscale, with dimensions on the order of nanometers (10^-9 meters). These ultra-small devices offer unique properties and advantages, including higher sensitivity, faster response times, and lower power consumption compared to their MEMS counterparts.
The Role of 3D Printing:
3D printing, or additive manufacturing, has emerged as a powerful tool for fabricating MEMS and NEMS devices with unprecedented precision and complexity. Unlike traditional microfabrication techniques such as lithography and etching, which are limited by their two-dimensional nature and substrate dependency, 3D printing allows for the creation of three-dimensional structures with arbitrary geometries and material compositions.
Advantages of 3D Printed MEMS/NEMS:
1. Design Flexibility: 3D printing enables the rapid prototyping and iteration of MEMS/NEMS designs, facilitating the exploration of novel geometries and functionalities. Design parameters such as shape, size, material properties, and surface features can be easily customized to meet specific application requirements.
2. Integration of Multiple Components: With 3D printing, complex MEMS/NEMS systems comprising multiple interconnected components can be fabricated as a single monolithic structure. This integration minimizes assembly steps, reduces part count, and enhances overall system reliability.
3. Material Versatility: 3D printing supports a wide range of materials, including polymers, metals, ceramics, and composites, offering flexibility in material selection for MEMS/NEMS fabrication. Advanced additive manufacturing techniques such as multi-material printing and in-situ material deposition further expand the design space and performance capabilities of micro-scale devices.
4. Scalability: 3D printing allows for the scalable production of MEMS/NEMS devices, from prototyping small batches to mass production of large quantities. This scalability is particularly advantageous for commercial applications requiring high-volume manufacturing and cost-effective production.
Applications of 3D Printed MEMS/NEMS:
1. Sensing: 3D printed MEMS/NEMS sensors find applications in a wide range of fields, including environmental monitoring, healthcare diagnostics, and industrial process control. These sensors offer high sensitivity, fast response times, and miniaturized form factors, making them ideal for deployment in compact and remote environments.
2. Actuation: MEMS/NEMS actuators fabricated via 3D printing enable precise manipulation and control of mechanical motion at the micro and nanoscale. These actuators are used in microfluidics, optical systems, and microrobotics for tasks such as valve actuation, mirror tilting, and nanopositioning.
3. Energy Harvesting: 3D printed MEMS/NEMS devices are being explored for energy harvesting applications, where they convert ambient vibrations, thermal gradients, or electromagnetic radiation into electrical power. These energy harvesters have potential applications in autonomous sensors, wearable electronics, and IoT devices.
4. Biomedical Devices: 3D printed MEMS/NEMS are revolutionizing biomedical devices such as lab-on-a-chip systems, drug delivery systems, and implantable sensors. Their miniaturized form factor, biocompatibility, and high precision enable new capabilities in personalized medicine, point-of-care diagnostics, and targeted therapy.
Future Directions:
As 3D printing technology continues to advance, so too will its applications in MEMS/NEMS fabrication. Future developments may include the integration of novel materials, such as 2D materials and bioinks, for enhanced device performance and functionality. Moreover, advancements in multi-material printing and nanoscale resolution techniques will further push the boundaries of micro-scale technology, paving the way for transformative innovations in electronics, healthcare, and beyond.
Conclusion:
The convergence of MEMS, NEMS, and 3D printing holds immense promise for the future of micro and nanoscale technology. By leveraging the design flexibility, material versatility, and scalability of additive manufacturing, researchers and engineers are pushing the boundaries of what is possible in sensing, actuation, energy harvesting, and biomedical applications. As the field continues to evolve, we can expect to see increasingly sophisticated and impactful MEMS/NEMS devices that drive innovation across diverse industries and improve the quality of life for people around the world.
Comments