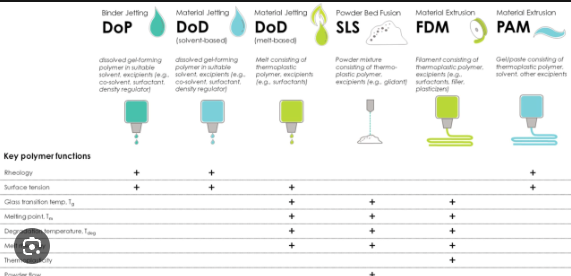
Introduction:
The world of 3D printing is vast and diverse, with a wide array of materials available for creating everything from prototypes to final products. The choice of base material plays a crucial role in determining the strength, durability, surface finish, and even the color of the printed object. In this blog, we'll delve into the various base materials commonly used in 3D printing, exploring their properties, applications, and considerations for selection.
1. Thermoplastics:
- ABS (Acrylonitrile Butadiene Styrene): Known for its strength, durability, and heat resistance, ABS is a popular choice for functional prototypes and end-use parts. It's commonly used in industries such as automotive, aerospace, and consumer goods.
- PLA (Polylactic Acid): PLA is a biodegradable thermoplastic derived from renewable resources such as cornstarch or sugarcane. It's favored for its ease of printing, low warping, and environmental sustainability, making it ideal for educational projects, consumer products, and food packaging.
- PETG (Polyethylene Terephthalate Glycol): PETG offers a balance of strength, flexibility, and chemical resistance, making it suitable for applications requiring durability and impact resistance. It's often used in engineering parts, mechanical components, and medical devices.
2. Thermoset Resins:
- Resin-based 3D printing, also known as stereolithography (SLA) or digital light processing (DLP), utilizes photopolymer resins that solidify when exposed to light. These resins offer high resolution, fine detail, and smooth surface finishes, making them ideal for intricate models, jewelry, and dental appliances.
- Types of resin include standard, castable, flexible, and dental-grade, each tailored to specific applications and requirements. Resin-based printing is commonly used in industries such as jewelry, dentistry, and prototyping.
3. Metals:
- Metal 3D printing, or additive manufacturing, utilizes metal powders fused together layer by layer to create dense, fully functional metal parts. Common metals used in metal additive manufacturing include stainless steel, aluminum, titanium, and nickel alloys.
- Metal 3D printing offers exceptional strength, precision, and geometric complexity, making it suitable for aerospace components, medical implants, automotive parts, and high-performance engineering applications.
4. Composites:
- Composite materials combine two or more distinct materials to create a hybrid material with enhanced properties. Common composite materials used in 3D printing include carbon fiber, fiberglass, and Kevlar-reinforced polymers.
- Composite filaments offer improved strength-to-weight ratios, stiffness, and impact resistance compared to traditional thermoplastics, making them ideal for aerospace, automotive, and sporting goods applications.
Considerations for Material Selection:
- Mechanical properties: Consider factors such as strength, flexibility, toughness, and heat resistance based on the intended application of the printed object.
- Surface finish: Different materials offer varying levels of surface smoothness and detail resolution, which may be important for aesthetic or functional purposes.
- Environmental considerations: Evaluate the sustainability, biodegradability, and recycling capabilities of the base material, especially for applications with eco-friendly requirements.
- Cost: Compare the cost per unit of different materials, considering factors such as material waste, post-processing requirements, and long-term durability.
Conclusion:
Base materials play a critical role in the success of 3D printing projects, influencing the performance, aesthetics, and functionality of the printed objects. By understanding the properties, applications, and considerations of different materials, designers and engineers can make informed decisions to optimize their 3D printing processes and achieve the desired outcomes. As 3D printing technology continues to evolve, we can expect further advancements in material science, offering even more possibilities for innovation and creativity in additive manufacturing.
Comments