
Additive manufacturing, also known as 3D printing, has transformed traditional manufacturing processes by enabling the creation of complex geometries with unmatched precision. One avenue of innovation within additive manufacturing lies in the utilization of composite materials. These materials, composed of two or more distinct constituents, offer unique properties and benefits when integrated into the additive manufacturing process.
Examples of composite materials commonly used in additive manufacturing include carbon fiber-reinforced polymers (CFRP), fiberglass-reinforced polymers (FRP), and metal matrix composites (MMCs). These materials combine the strength and stiffness of fibers or particles with the versatility and formability of polymers or metals, resulting in enhanced mechanical properties and lightweight structures.
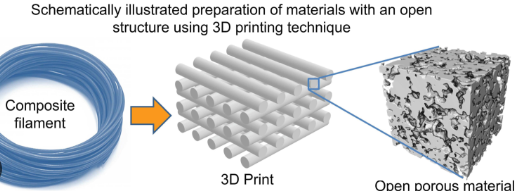
Pros of integrating composite materials in additive manufacturing:
1. Lightweight: Composite materials are renowned for their high strength-to-weight ratio, making them ideal for applications where weight reduction is critical, such as aerospace and automotive industries.
2. Customization: Additive manufacturing allows for the precise placement of reinforcing fibers or particles within a polymer or metal matrix, enabling tailored material properties to meet specific performance requirements.
3. Enhanced performance: Composite materials offer superior mechanical properties, including high tensile strength, stiffness, and fatigue resistance, compared to traditional materials like metals or plastics.
4. Design freedom: Additive manufacturing enables the creation of complex geometries that are challenging or impossible to achieve with conventional manufacturing methods, providing designers with unprecedented freedom in product design.
Cons of integrating composite materials in additive manufacturing:
1. Cost: Composite materials can be more expensive than traditional materials, particularly high-performance fibers like carbon fiber. Additionally, the equipment and processes required for additive manufacturing of composites may incur higher initial investment costs.
2. Processing challenges: Achieving optimal dispersion and alignment of reinforcing fibers or particles within the matrix material can be challenging, affecting the mechanical properties and consistency of the final product.
3. Post-processing requirements: Some composite additive manufacturing processes may require additional post-processing steps, such as curing, machining, or surface finishing, to achieve desired mechanical properties and surface quality.
In conclusion, the integration of composite materials in additive manufacturing offers significant opportunities for innovation and performance enhancement across various industries. While there are challenges to overcome, the benefits of lightweight, customizable, and high-performance structures make composite additive manufacturing a compelling avenue for future advancements in manufacturing technology.
Comments